Testing Heat Shields for Various Environments
- Chethana Janith
- Nov 13, 2024
- 3 min read
Chethana Janith, Jadetimes Staff
C. Janith is a Jadetimes news reporter covering science and geopolitics.
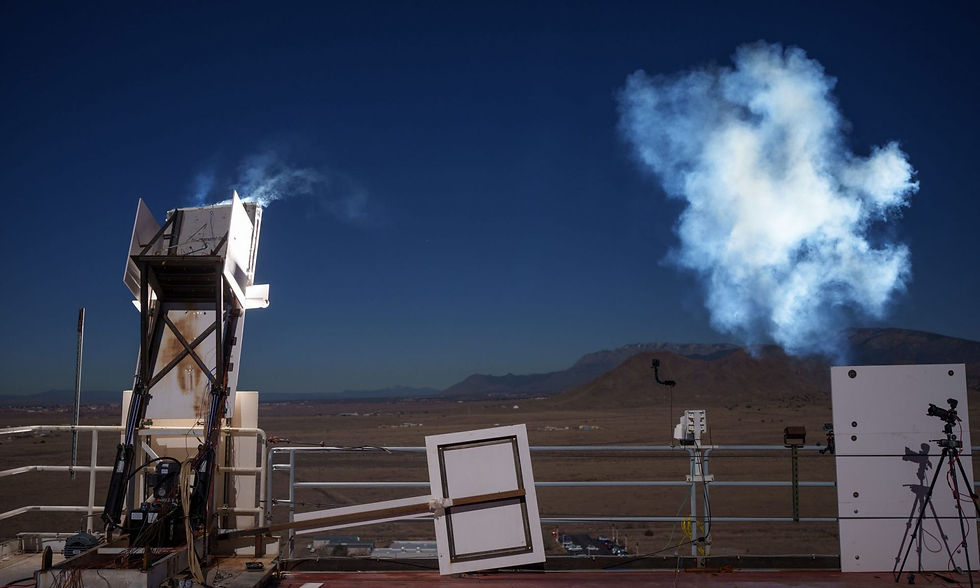
Testing is one of the unsung steps in the engineering process. Talk to any product development engineer, and they will tell you how big of a milestone passing “V&V” – or verification and validation – testing is. Testing is even more critical when you work on equipment meant for the harsh space environment. It is also more challenging to mimic those harsh environments on Earth. Luckily for some of NASA’s more critical upcoming missions, another government agency has a unique test lab to help V&V with some of its most critical components – their heat shields.
That other government agency is the US Department of Energy (DoE), specifically its Sandia National Laboratory. The US’s national labs were initially developed to coordinate nuclear weapons research, but they have since taken on a broader role in the country’s fundamental scientific research efforts. That includes providing test equipment unavailable anywhere else in the world.
One unique test setup at Sandia is known as the solar testing facility. It’s a field with over 200 “heliostats” – giant mirrors that can focus the light from the Sun that they reflect on a particular point. With all of them focused on the same point, it can get as hot as 3,500 times the typical sunlight on an area.
Credit – Sandia National Labs YouTube Channel.
That area is also one of the selling points of the solar testing facility. It can test pieces of material up to 1 m (3 ft) in diameter. This makes it superior to other test facilities that intend to test the same types of materials, such as those that use arc jets or lasers. Cost is also a consideration, with arc jet or laser testing costing more than $100,000 daily. Comparatively, solar testing costs only $25,000 per day, mainly due to the lower energy costs of operating the heliostats.
NASA has used all of that testing technology over the last year to test the heat shields of some of its most important missions – the Mars Sample Return (MSR) mission and Dragonfly, the helicopter mission to Titan. Each mission has its challenges, but the materials for their heat shields are the same. Known as a Phenolic impregnated Carbon Ablator, this material has already been successfully used for missions such as Stardust, OSIRIS-REx, and Mar Science Laboratory.
MSR and Dragonfly each have unique challenges that other missions didn’t face. MSR will be carrying a significant payload of samples back to Earth, meaning it will be heavier than the OSIRIS-REx asteroid sample return mission. It will be so heavy that some NASA engineers intentionally bent the test material at Sandia’s test lab to model what happens to material undergoing the force of reentry.
Credit – BPS.space YouTube Channel.
For its part, Dragonfly has to deal with a world with a much thicker atmosphere than Earth itself. Titan’s atmosphere is four times denser than Earth’s. Given the interplanetary speeds at which the mission will be traveling when it reaches orbital insertion, Dragonfly’s accompanying lander will be subjected to both high heat and pressure as it descends onto the Moon’s surface.
Sandia’s lab technicians made a number of improvements to the test setup for the tests, including running gas lines to the sample from the base of the tower to better mimic the atmosphere the heat shields will be encountering. They were also on hand to help with troubleshooting, which included multiple instances where some fiber surrounding the sample caught fire before the test could be completed.
V&V testing rarely completes without some adjustments and occasionally without any fires. Testing on this type of setup is just part of NASA’s test plan for the heat shield use case, with other tests happening elsewhere. Given the importance of this particular material to the overall success of these critical missions, the more testing they are able to undergo here on Earth, the better.
Comentários